ABOUT US
PROUDLY MADE IN ITALY SINCE 1965
The Company, founded in 1965 as Zatti Arredamenti Snc, assumed a new corporate identity with the birth of Zatti Interiors Srl in 2017.
This italian family history began in 1965 with the intuition of three brothers.
For decades it has seen the strong leadership of Lorenzo Zatti and today his son Giovanni is on the pilot bridge, always with a
common thread: the will and pleasure of making and building every day something unique and special.
Completeness and versatility
are today the combination that guide the work of Zatti Interiors, looking ahead to the future and expressing a new flow of
energy in housing and daily living.
Throughout its history, the Company has developed an extraordinary ability to deliver eclectic
versatile achievements. Always with the highest profile and quality level, the Company can range from the design and construction of:
public places (hotels, restaurants, museums, exhibition stands), prestigious private residences (villas and apartments), commercial retail
stores (flagship and mono-brand), naval furnishing (both private yachts and cruise ships).
We take pride in the pursuit of a policy
that has its main pivot foundation in the ability of internal making.
Years of working together have also led to the selection of
a reliable group of companies that support Zatti Interiors in various areas (marble and stone, textiles, glass, metals processing, ...).
We have grown over the years a number of extraordinary relationships with world-renowned architects, with whom our
Company has had over the years the honor and the ability to collaborate. Somenames: Jean-Michel Wilmotte, Norman Foster, Marco Piva, Fred Genin,
Simone Micheli, Adam D. Tihany, Massimo Iosa Ghini.
We possess a limitless ability to manage orders around the world. We can
match the needs of our customers beyond the geographical context and differences in style because Italian craftsmanship not only
shows a 'know-how', but also a 'know-to-interpret', quite typical of our ability to work 'taylor-made' and 'projects-based'.
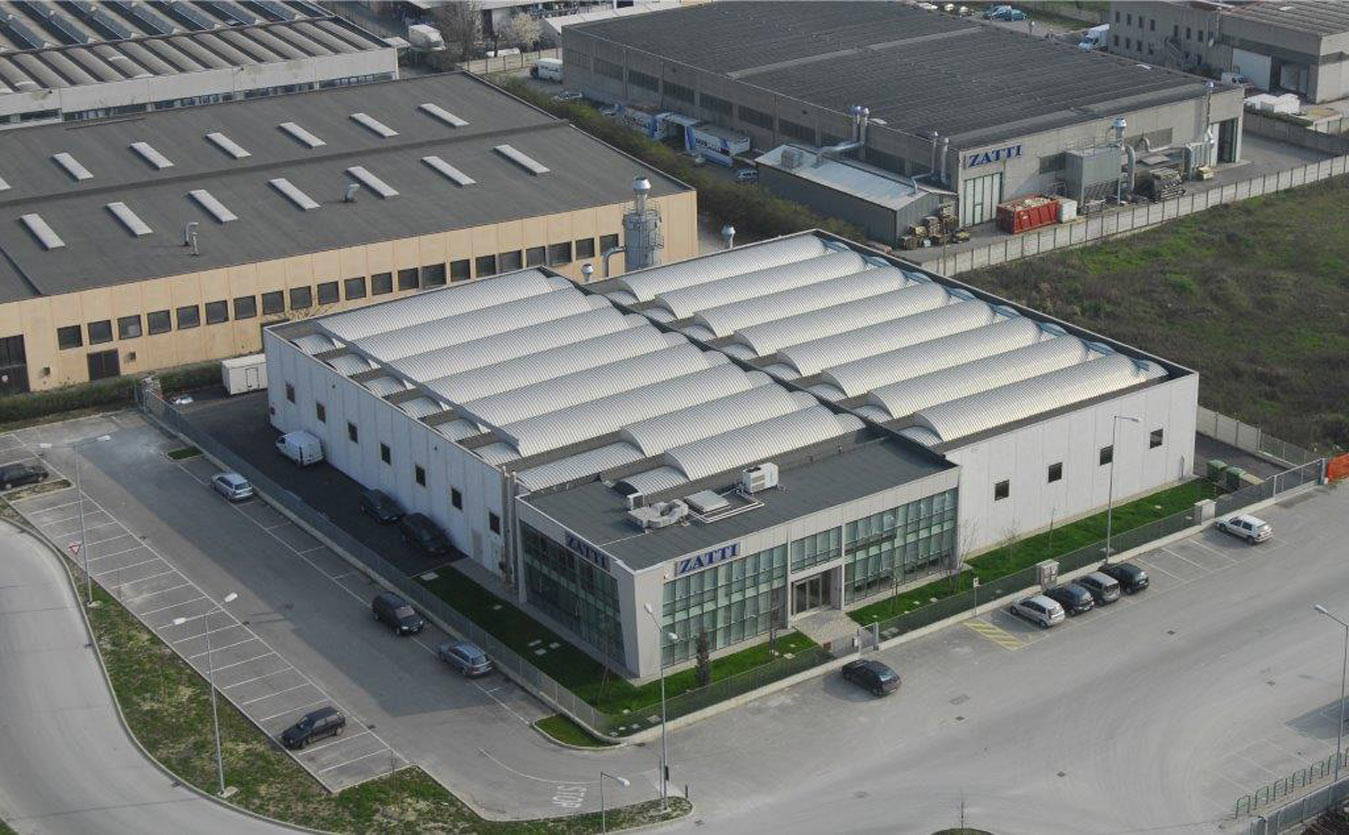
CARE FOR ENVIRONMENT
For Zatti Interiors these are not just empty words: many efforts and investments have been made in recent years to update the
company to avant-garde environmental standards.
Some examples: the purchase of raw materials (wood and wood-based semifinished products) only includes those with certification (PEFC, FSC, PPT),
the painting processes is eco-friendly and uses also water paints without solvents, and last but not least we carefully manage the disposal of the
various waste products exclusively with certified companies specialized for the industry.
A real Company's flagship is then photovoltaic system installed on the roof of one of its factories, with a total area of approximately 3,000
sqm and a total capacity of 300 kWp. This system makes the Company fully independent in terms of power consumption and in addition it allows to
sell to the public network the power exceeding own needs.
Concurrently with the realization of the photovoltaic system we have carried out the requalification of the building itself by replacing the
old covers containing asbestos with new materials, thus obtaining also a substantial improvement in terms of thermal dispersion and acoustic insulation.
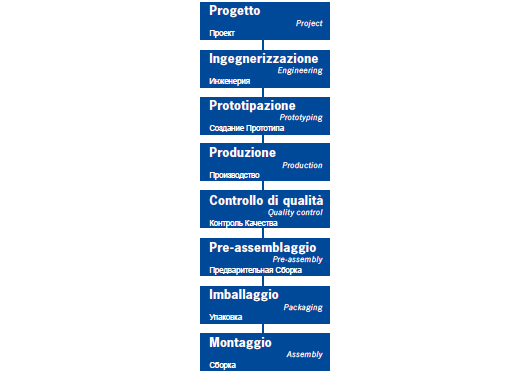
PRODUCTION PROCESS
In almost half a century of experience, the Company has grown and changed: from the small family workshop
started in 1965, it has becomes a dynamic and industrialized enterprise, combining the experience and the strong tradition of
carpentry with the most innovative and advanced technology. Zatti Interiors has a production facility of 5000 sqm, together with
600 sqm of administrative, commercial and technical offices.
From conceptual design to solution engineering, from production to assembly, every detail is 'sewn' on the client. An additional
proof of the Company constant pursuit of perfection is the Quality System UNI EN ISO 9001:2008 Certification gained since 2005.
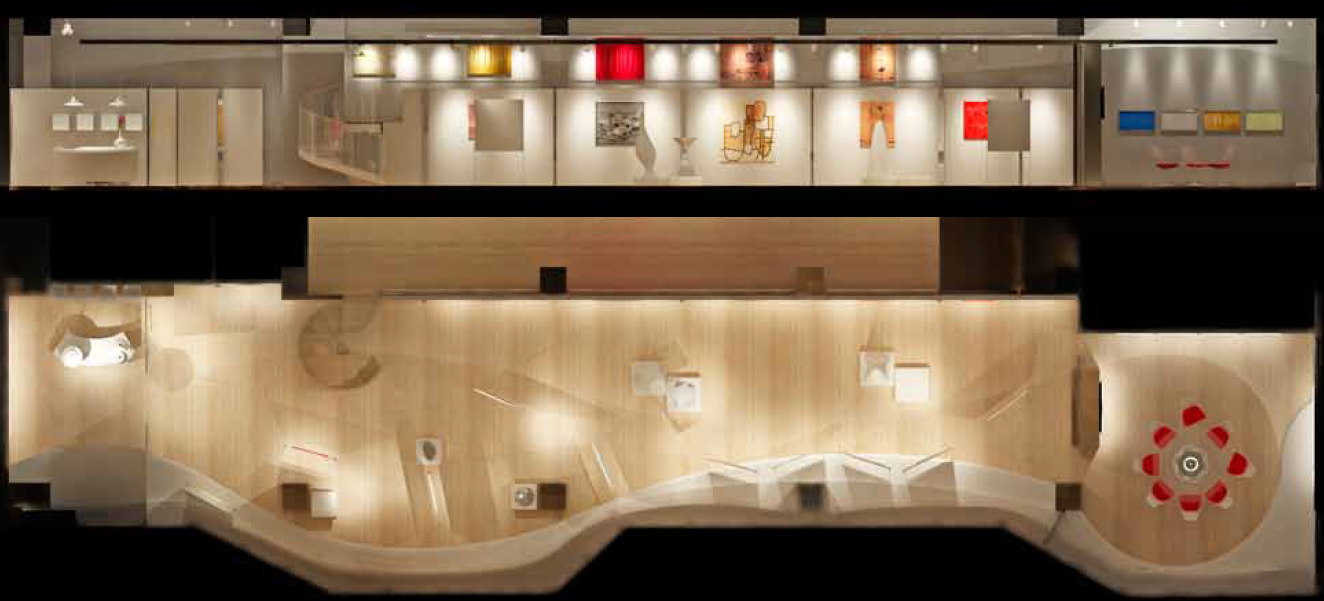
PROJECT, ENGINEERING AND PROTOTYPING
Our ability expands in different directions. Mainly we are committed to serve our Customers and Architects from whom
we receive initial projects and concepts that we then develop and engineer in our internal 'Design and Engineering' office. The ability
of our experienced team of architects and engineers to work in synergy with the customers and the architects signing the
projects is widely appreciated and it is definitely a real key success factor of the Company. The continuous
exchange and flow of information allows to improve, and thus guarantee, the execution feasibility and the most careful and
appropriate selection of materials best suited to the construction of the final products.
A well-established ability of our 'Design and Engineering' department is also the development of original proprietary project proposals starting
from specific requirements and needs expressed by our customers. In this case, the use of advanced 3D rendering programs
together with the manual ability to design and sketch (still irreplaceable) are a real strength in our Company. The result of
this work in terms of executive design, leads to the creation of prototypes (mock-up) often essential to the understanding
of the product and to its improvement before proceeding to the actual production phase.
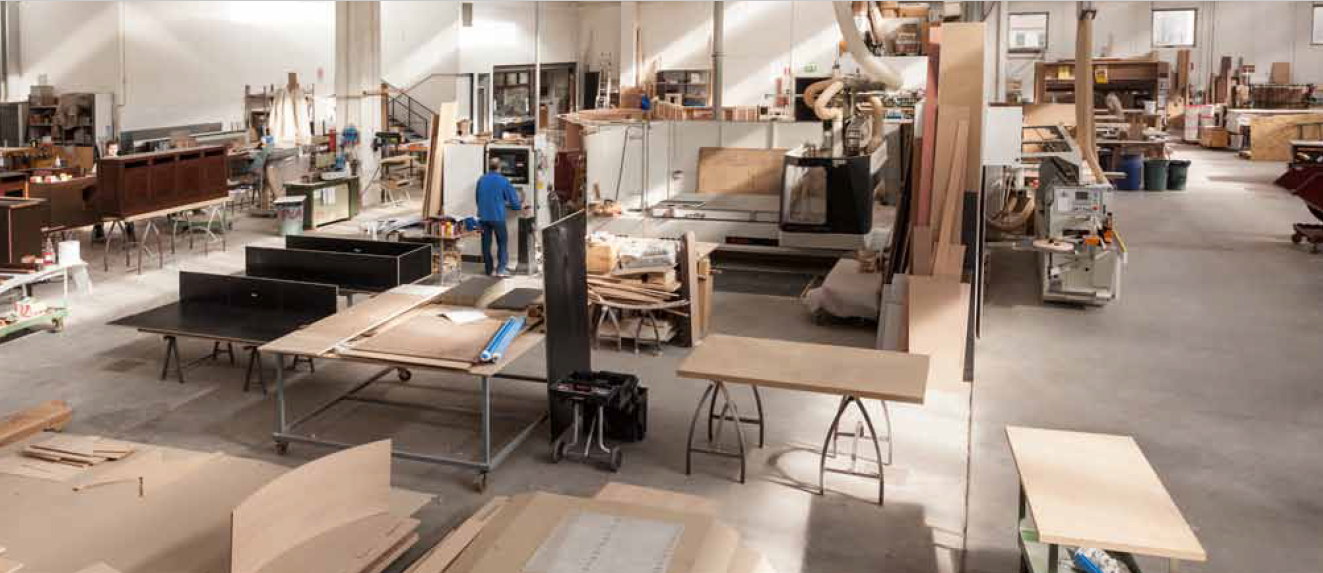
PRODUCTION
The first phase of production is based on a careful and skilful selection of raw materials, as the purchase of wood and
semi-finished products must be carefully evaluated according to the characteristics of the furnishings that must be delivered. This is especially
true today because the requirements for certifications, local packaging and special use purposes (e.g: fire resistance classifications, moisture and
water resistance, other specific regulations at the national level) are a pre-requisite standard for every order especially when operating at
international level. The Company is internally organized to be able to handle every phase of the wood work: cutting, veneering and pressing until
the final painting, using a complete line of machine tools both CNC and traditional, both state-of-art and always updated. In particular the internal
pressurized spray cabin allows the layering of a wide range of paintings and lacquering. A feature historically present in the company is the
presence of an internal department for metalworks (stainless steel, iron, brass, aluminum) managed by a dedicated and especially trained team.
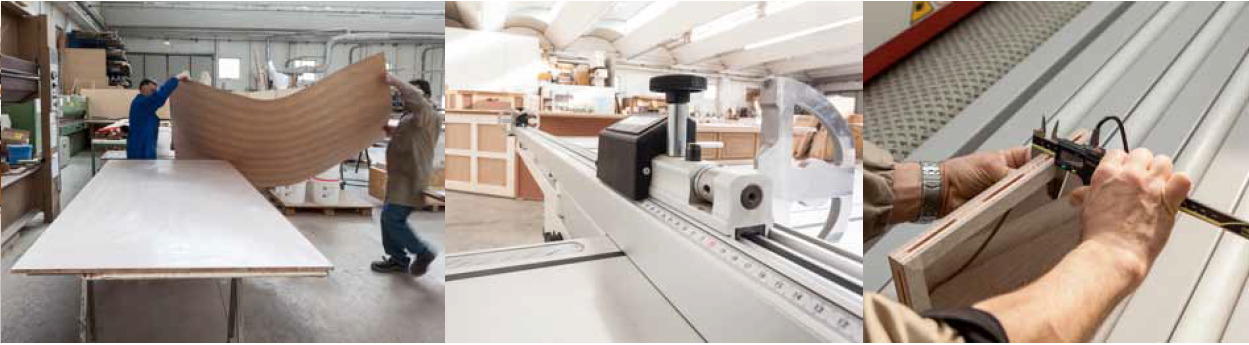
QUALITY CONTROL
A careful and strict control system awards to the final product of Zatti Interiors the highest quality standard.
The certification, based on the UNI-EN ISO 9001:2008 Quality System, will ensure compliance with the rules defining the implementation requirements
of a quality management system, for the management of the business processes, the improvement of the effectiveness and efficiency in the production
and in the delivery of the service, in order to meet and increase customer satisfaction. For our Quality System, the Company relies on ICILA, the
Italian Certification Authority that operates specifically in the field of decor, furnishings and of wood industry. Being certified is synonymous
with professionalism, ensuring control over the supply and quality assurance of used materials.
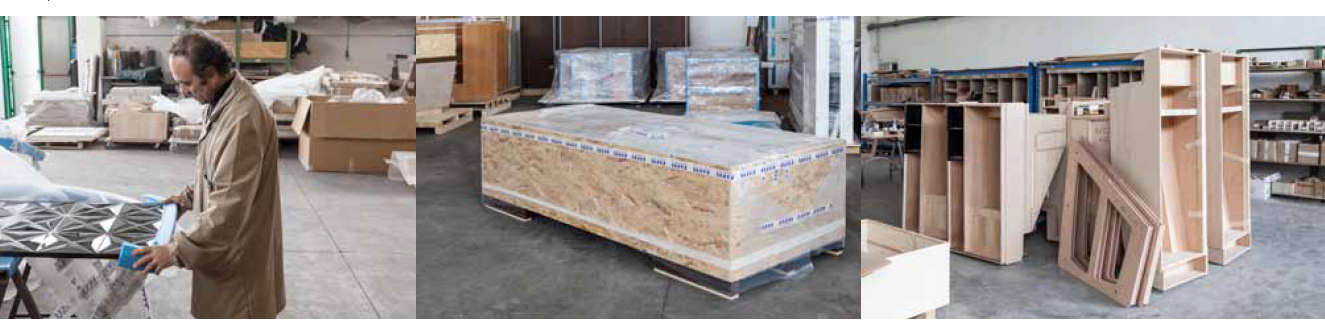
PACKAGING
At the very end of the production process, we enter a very delicate phase. Only the attention to detail and experienced perception
can lead to accurate level of packaging.
Every choice and arrangement ensures and preserves the finished piece during transportation.
Negligence at this stage would prevent Zatti Interiors to work for international clients, and all the attention devoted during the previous phases
would become useless.
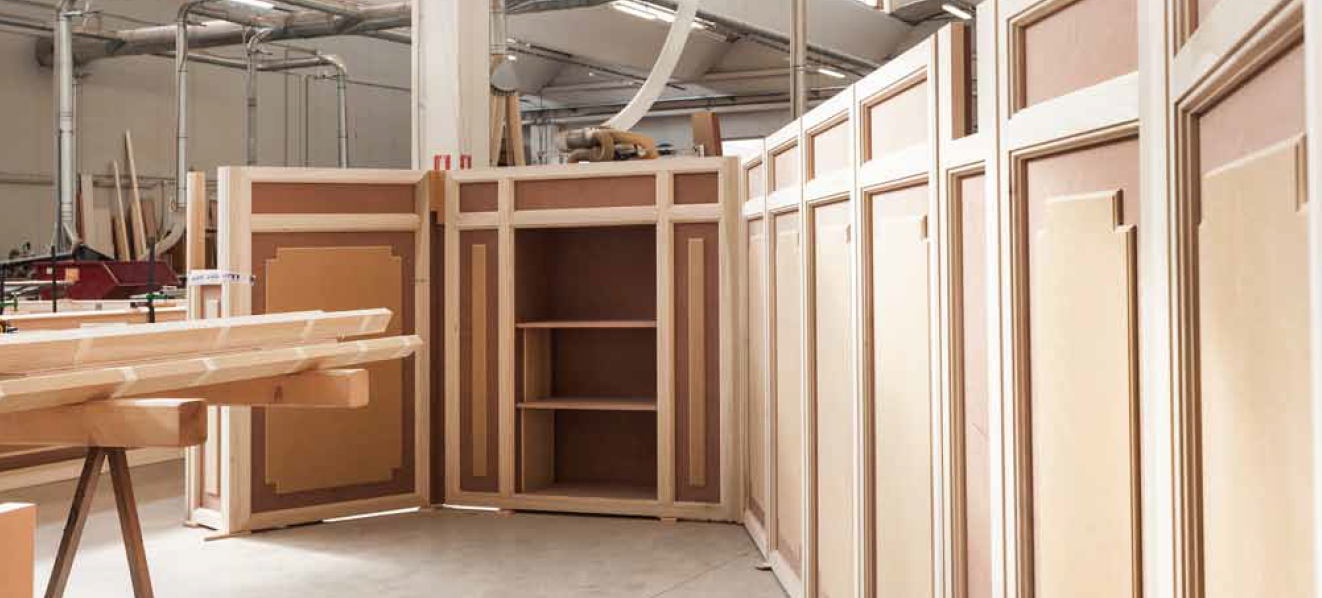
PRE-ASSEMBLY
Once the production is completed, we always proceed to the pre-assembly of the works in order. This is a really
exciting phase greatly appreciated by Architects and final Customers: inside our large assembly spaces, all that has been produced both internally by
the Company and externally by third parties suppliers (marble, glass, textiles, metals, ..) is perfectly composed as in a huge puzzle. The pre-assembly
allows the verification and the possible adjustment of all parts of the industrial product, sometimes very complex, prior to shipment. This
guarantees, in addition to the attention paid to every design and manufacturing phases, be sure to send a perfect product to the yard of destination.
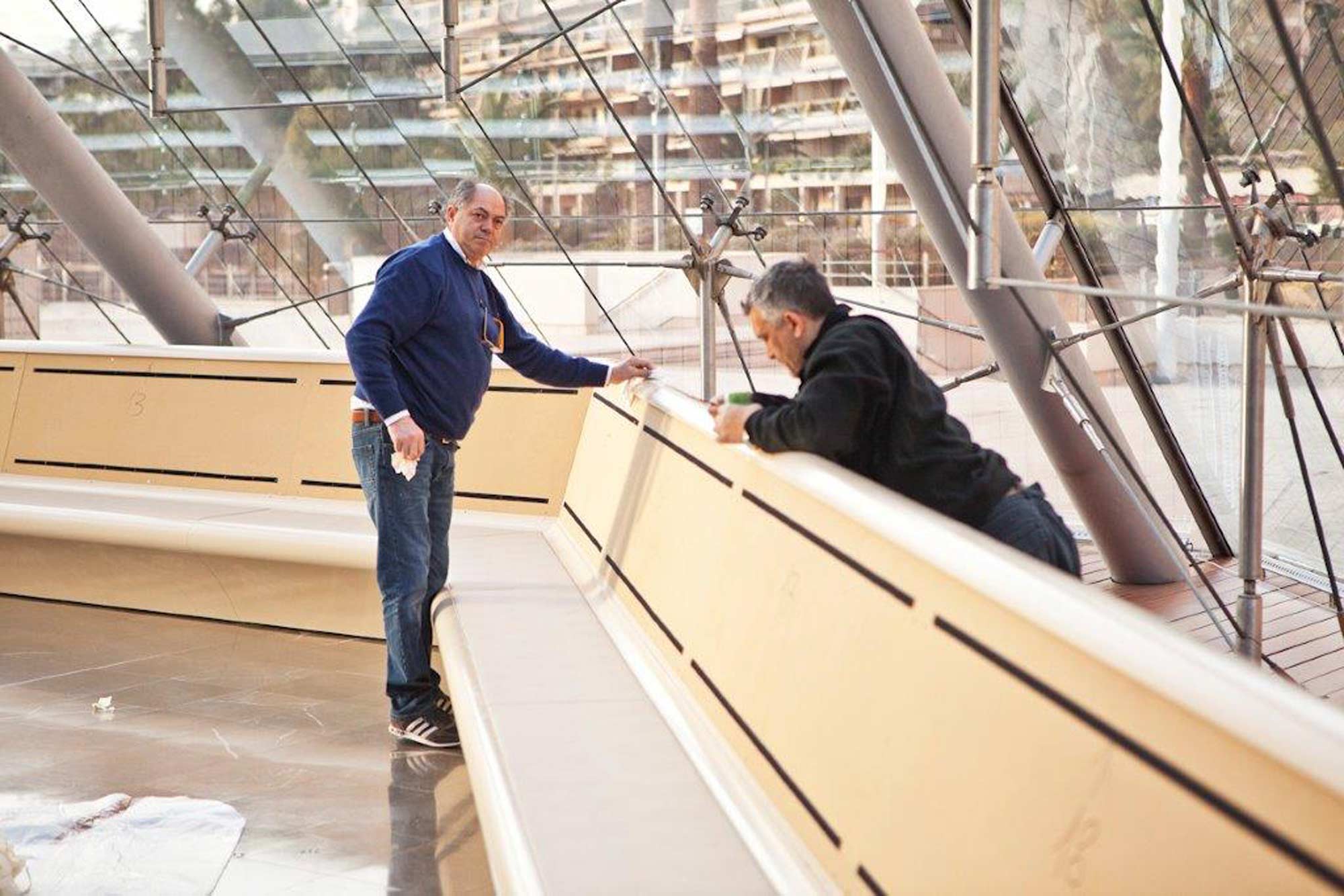
ASSEMBLY
The final test, the demonstration that what happened so far has generated and correctly interpreted 'the idea', puts a strain on a
team of skilled installers, the natural extension of the Company's internal design team and production. They are interpreters themselves of the
wishes of the customer and often work in symbiosis with the end user.
The hard work and the complexity of the production process of each piece done so far is entirely placed in the hands of our skilled installers.
The Company strongly believes that a good product needs to be optimally installed, and this applies in particular to the special achievements and
tailor-made works that are most of the time our operational standard.